- Tips
- technology
- Frequently Asked Questions
- Tests
- mAh capacity
- Rated Capacity
- everActive
- comparison
- Durability of rechargeable batteries
- Efficiency of rechargeable batteries
- battery voltage
- Accumulated energy
- Batteries vs rechargeable batteries
- LR03 AAA
- LR6 AA
- eneloop
- AG13 LR1154 LR44
- Delta V
- Charge Cycles
- internal resistance
- charge level
- CR 2032
- memory effect
- accredited test
- SR44 357
- Hearing Batteries 675
- SR626 377
- Watch Batteries
- Polarity
- Mah
- passivation
- LS 14250
- LS 14500
Another great study of battery and rechargeable battery performance? - Watch out for the 7 deadly sins committed by testers. When is a test reliable/valuable? Check out our cheat sheet.
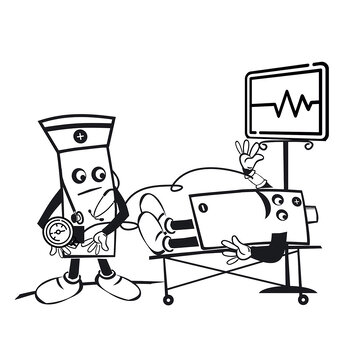
In my opinion, the above problem does not result directly from "sponsoring" tests or attempts to influence their results. In most cases, oversights and mistakes made by testers and reviewers are definitely to blame.
We point out regularly repeated mistakes that can easily undermine the reliability of most tests found on the Internet.
Highly random test conditions → lack of reproducibility of results
Comparable, reproducible test conditions are perhaps the most important starting point for any comparative study. Unfortunately, the most common mistake made by testers has its genesis at this root.
For example, a typical AA/AAA LR6/LR03 alkaline battery tester often has an advanced "machine" - a precise electronic load, where you can set the discharge current/discharge power with high accuracy, or simulate any load resistance. The batteries to be tested are placed in the basket, the basket is connected to the load and the measurement is carried out.
And here comes a non-obvious problem – typical battery baskets/holders are designed for very low loads. After applying loads such as 300 mA and higher, the voltage drops on the springs, clamps, and finally on thin test leads are so large (sometimes reaching tenths of a volt) that the percentage differences in the obtained operating time / measured capacitance can reach double-digit values. In such configurations, even obtaining the same results in subsequent repetitions of the test of the same battery is very difficult. With measurement errors of 10% and higher, comparing the results loses any sense.
The solution to this problem is to use a high-current basket/holder and to lead four test leads (separate paths for voltage and current measurement), where the voltage measurement point is placed as close as possible to the poles of the tested battery. How many times have you seen it done in such a configuration, with 4 test leads? Just like me – probably rarely or perhaps not at all.
In a typical popular test, even the best, most precise electronic load will not help if we do not ensure that the voltage is measured reliably directly from the battery. In a typical test scenario for AA/AAA cells, a low-cost branded charger with discharge and capacity measurement function will provide more repeatable test conditions.
Inconsistent selection of test/measurement equipment
The equipment you have for testing batteries and rechargeable batteries does not have to be expensive or complicated – many testers have expensive and precise equipment, which, if used incorrectly, will turn out to be less useful than a simple dedicated charger with a capacity measurement function. In the simplest test, all you need is a simple resistor with known resistance, a digital multimeter, and the recording of elapsed time and voltage at specified intervals.
It is important that the test conditions correspond to the nature of operation/the specifics of the tested batteries. For example, even the most precise measurement of the discharge of Ni-MH batteries will not be of any use if we do not take care of their proper charging / formation beforehand. Having the most precise discharging device possible, we must take care of equally good equipment, reliable connections and a decent charger when testing batteries.
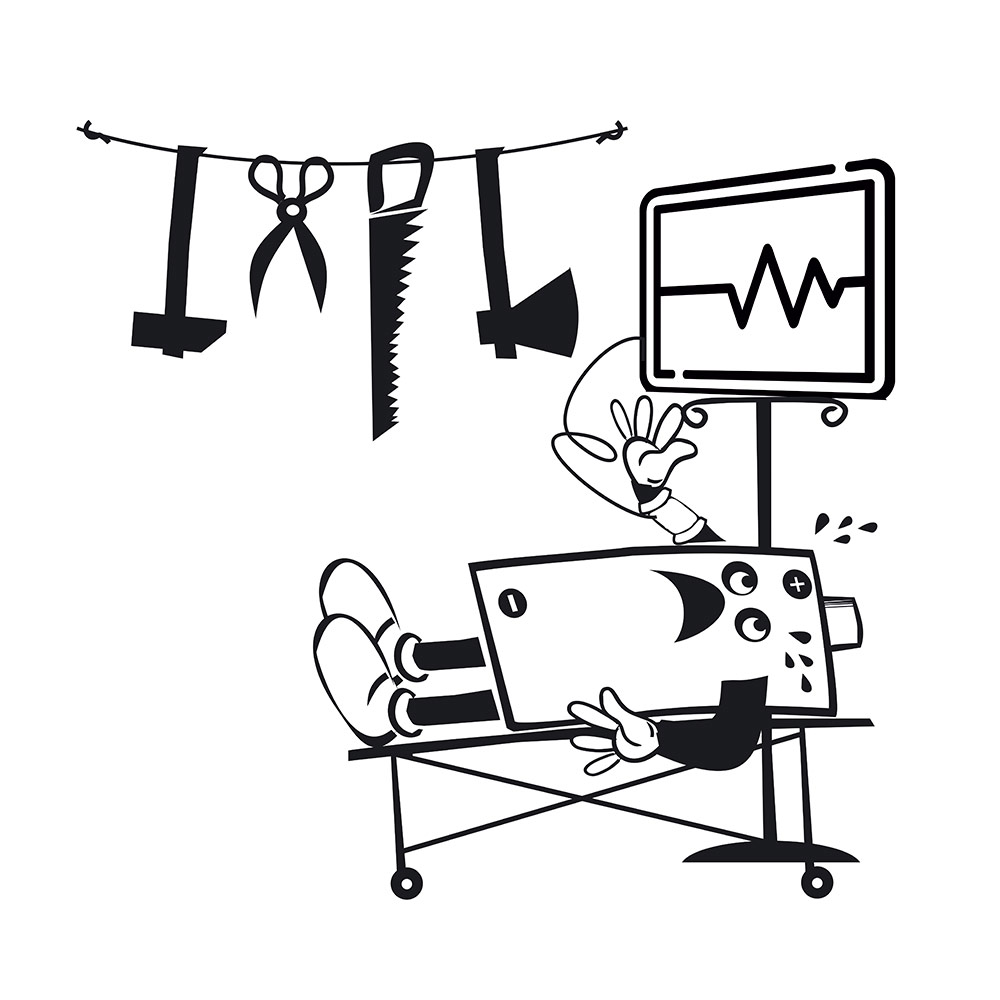
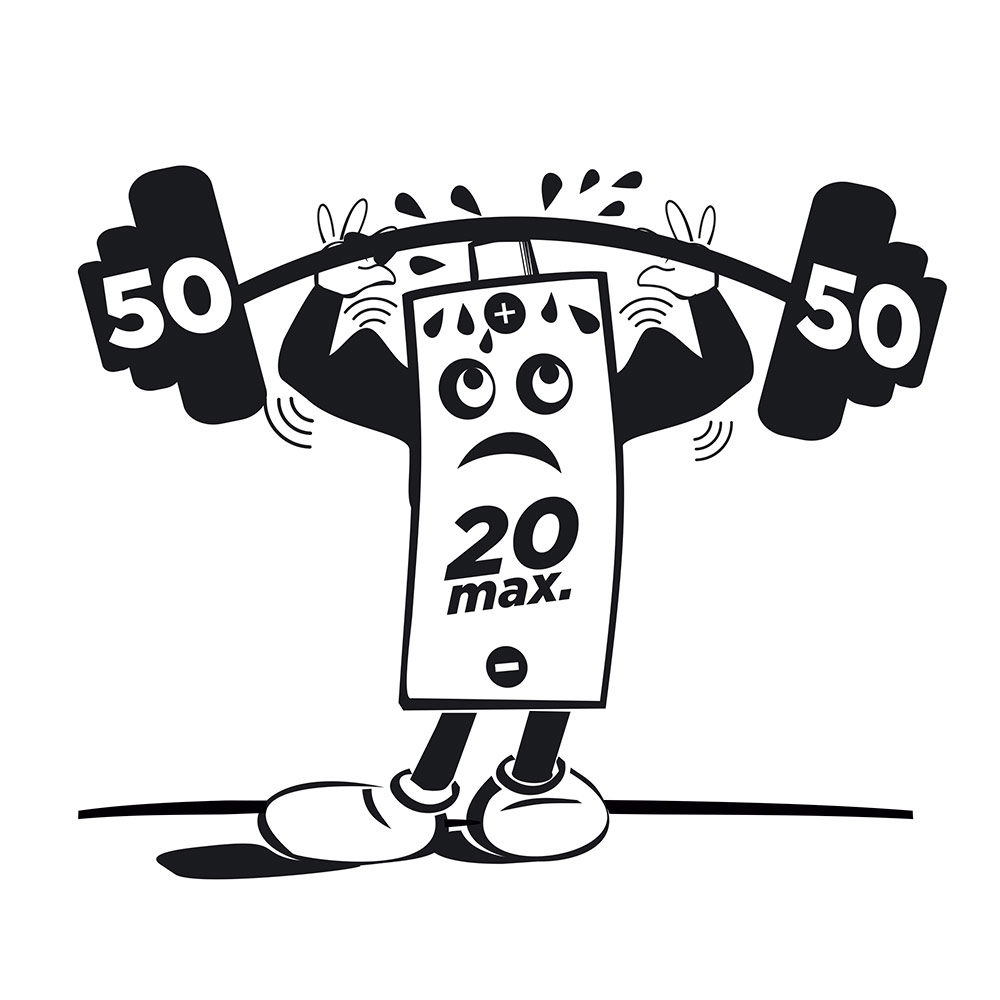
Rush to test
An editor doing a test for the next issue of a newspaper, etc. is bound by specific deadlines within which it must fit into the preparation of tests. The same applies to YouTubers who count on high viewership and want to start making money on their materials quickly. Unfortunately, the visible haste, the lack of a specific, repeatable test procedure is typical in most tests that can be found on the Internet.
An obvious example is, for example, measuring the energy and capacity of CR2032 disposable batteries under a continuous load of more than 5 mA – where such conditions are beyond their nominal capabilities. Certainly, not everyone wants to waste a few days on testing one battery, but in the case of some batteries, it is simply impossible to do otherwise – the use of too high loads causes the batteries to work in abstract, unacceptable conditions – the result is a lack of repeatability of results, even within the same batteries, a significant spread of the measured capacity between tests and, of course, unrealistic, very underestimated results of such a test for most products.
No information about the age of the tested rechargeable batteries
Unfortunately, testers often lack basic knowledge about the products they are testing.
Even the highest quality specialist, an electronics engineer who has the appropriate equipment to perform tests, who knows how to take care of the lowest possible measurement uncertainty, will not carry out the test properly if he does not take care of products manufactured in a similar period.
The permissible permanent degradation of new, unused Ni-MH batteries can reach up to 30% after just 12 months from the original full charge. Of course, none of the branded rechargeable batteries ages so quickly, but especially the most capacious rechargeable batteries clearly age over time, no matter how intensively they are used.
The same applies to alkaline batteries, where, depending on the storage conditions, they can lose from 3 to 10% of their capacity per year, and their voltage characteristics deteriorate (such cells reach a lower voltage and give off less energy).
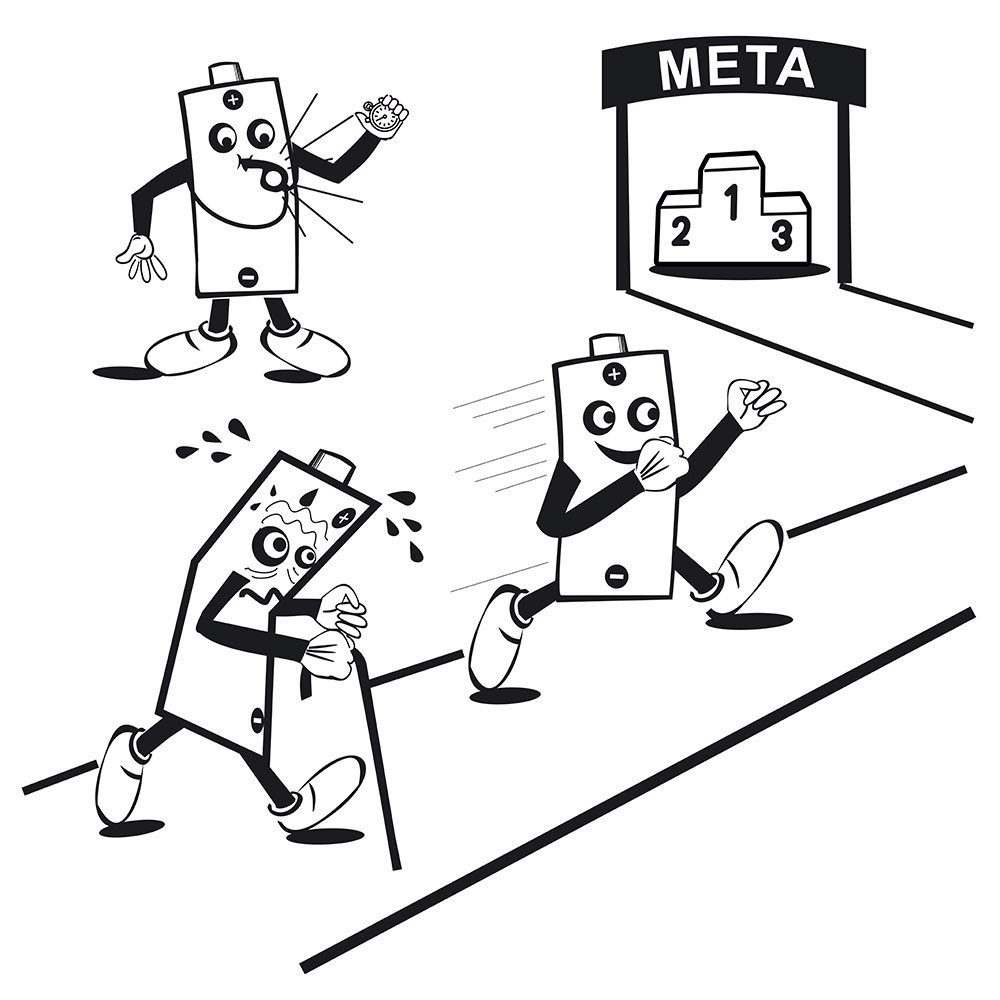
Test of storage deckchairs / defective items
This is a consequence of the previously described problem, where the tester did not even take care to check/verify the age/date of production of the tested cells.
In extreme cases, the tester gets deckchairs, dependent cells, where the part may be defective from the start. If the test procedure does not provide, for example, for checking the voltage level before the measurement or, in the case of rechargeable batteries, measuring the factory charge level before the first charging process, the tester does not even know whether it has not come across old or simply defective units.
Comparing the results of old, sometimes defective cells against new, selected ones completely misses the point and one can only hope that it is not a deliberate manipulation.
With 2-3 year old deckchairs, capacity losses of 20% and much less predictable operation are typical – the above applies to virtually all disposable batteries and rechargeable batteries available on the market.
As in the case of typical electronics, there can also be defective units in batteries and rechargeable batteries – logic dictates that they should be complained about, not tested...
Test procedure – or rather the lack of it
Looking through most of the tests, you can get the impression that the author decided that he has the perfect equipment for testing batteries/rechargeable batteries and nothing stands in the way of conducting such a test.
The result of many such tests is, for example, the lack of any procedure for forming Ni-MH batteries, or the use of an inappropriate charger, etc.
Ni-MH batteries, depending on their age, capacity, manufacturer, may require several cycles of full charge and discharge in order to form properly.
The target characteristic, the level of voltage during discharge develops gradually over time on Ni-MH batteries – therefore it seems necessary to carry out at least a few overcharges of the battery to have any comparative value.
For new rechargeable batteries (not deckchairs), the standards allow for measurement during the first 5 cycles.
In some popular tests, rechargeable batteries are charged only once or twice. They are charged on equipment that does not say much about the correct charging of the batteries installed in it.
The process of proper charging of Ni-MH batteries is crucial for further testing, even in a typical utility test, where a given reviewer/tester has only one automatic charger. Unfortunately, we are very uncertain whether all rechargeable batteries are treated equally and whether they have been properly charged. Especially when the process is not repeated several times.
In the absence of a sufficiently good charger, in the case of Ni-MH cells, a fair solution is to "manual" charge the batteries in accordance with the PN/EN/IEC 61951:2 standard, where the battery discharged several times to 1.0V is charged for 16 hours with a constant current of 10% of its capacity.
The process of testing, for example, LR6/LR03 alkaline batteries is at least theoretically simpler – although even there we usually see tests with loads of 300 mA-500 mA, in addition to the dubious quality baskets we wrote about in point 1. These are conditions in which such a battery has no chance of reaching its nominal capacity – the results will always be much lower, sometimes unpredictable. Such a test will not give clear information about the quality of a given battery. Unfortunately, there are much fewer tests with a load of e.g. 30-50 mA, which is a pity.
The testing process of Li-ion 3.6/3.7V batteries should also start with a good charger that will provide each battery with identical test conditions, preferably one where the maximum charging voltage is in the range of 4.18-4.22V.
When discharging such batteries, it is worth conducting tests with higher current values, such as 3A/5A/10A, and even 20A in the case of high-current batteries – here it is even more important to have a very reliable connection between the battery and the load and an uninterrupted voltage measurement as close as possible to the cell contacts.
Capacity measurement – the only right measure of battery or battery performance?
The vast majority of tests we deal with are based on synthetic capacitance measurement. We will skip here situations where the assumptions of such measurements are wrongly selected, or where the values of charging capacity are compared (we write about the correct measurement of capacity in another post) – unfortunately, even where the entire test was carried out, it would seem correctly, there is room for a big mistake